Emergency Tree Service Richmond VA involves the timely and careful removal of trees in a crisis. Services offer 24/7 availability and provide prompt site evaluation, ensuring that safety measures are taken to protect people and property.
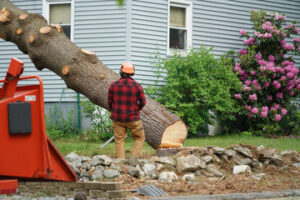
Look for an arborist with a good track record and certifications to ensure quality work. Moreover, check their insurance and liability coverage in case of any damages during the process.
Trees can add beauty and value to your property, but they can also pose a threat if they’re damaged or diseased. Emergency tree service can help you remove dangerous trees and branches before they cause damage or threaten safety. A well-established company with a solid track record can provide the peace of mind that your property is in good hands.
Some examples of emergency tree removal services include removing broken branches or trees, addressing storm damage, and removing dead or dying trees. Unstable trees are another common reason for emergency service, as they can be easily blown over by high winds and pose a risk to people and structures nearby. In some cases, it may be necessary to remove a tree entirely if it’s in danger of falling over.
The best way to prevent these problems is through regular maintenance. This includes trimming, pruning, and inspections. A professional arborist can help you decide when these tasks need to be performed and how often they should be completed. These professionals have a deep understanding of tree physiology and the impact that environmental conditions can have on tree health. They will also know when to apply the safest methods for tree cutting and removal.
When choosing an emergency tree service provider, look for one that is ISA (International Society of Arboriculture) certified. This is a strong indicator that the company adheres to the highest standards of quality and professionalism within the industry. It’s also important to assess a potential tree service provider’s experience with emergency situations, as this can indicate how they handle stress and unforeseen challenges.
An overgrown or damaged landscape can lead to increased home maintenance and cost, but a professionally maintained yard can increase the speed and ease of selling your property in the future. This is why it’s important to set up a maintenance budget for the unexpected, including emergency tree care services. A few small contributions over time can alleviate financial stress when a disaster strikes. In addition, a proactive approach to maintenance can prevent emergencies from occurring at all, protecting your property and preserving its value.
Tree Trimming
Whether the result of a storm or simply age, damaged trees and large branches pose serious hazards to people and property. Immediate removal by emergency tree service can prevent further damage and prevent potential injury. Additionally, prompt removal can help with insurance claims for property damage related to a hazardous tree. Emergency tree trimming is a highly specialized field that requires an experienced and knowledgeable team.
Often, a tree’s appearance alone can signal a need for immediate emergency tree services. Look for obvious damage such as broken branches, bare leaves or extensive fungal growth. Also, watch for a leaning tree that is more than 15% of its normal height or a hollow trunk. These signs indicate that the tree is weakened and can fall at any time, potentially damaging your home and posing a safety hazard to your family.
Many homeowners don’t realize that there is a need for emergency tree services until the situation is too late. If a tree or large branch falls on your house, it can cause significant damage that could require costly repairs and even lead to injury or death. Having a 24-hour emergency tree service available can be the difference between avoiding property damage and needing expensive repairs.
Trees are beautiful additions to any landscape, but they can become a nuisance when they are overgrown or show signs of neglect. Overgrown trees are unsightly and can block views, create privacy issues or even cause structural damage to your home. Emergency tree services can remove any unwanted trees or branches and help your yard return to its original beauty.
During a storm, trees can suffer significant damage, either from high winds or even just the weight of snow and ice. Trees that have sustained damage during a storm may have limbs or branches that are hanging precariously, making them a safety hazard for people and pets. Additionally, damaged trees can cause damage to nearby structures and power lines. Fortunately, 24-hour emergency tree service can handle these situations quickly and effectively to prevent further property damage and injuries.
Tree Pruning
Tree trimming is the process of removing dead, diseased or weakly attached branches to promote growth and enhance appearance. Generally speaking, pruning should be done on a regular basis to maintain plant health, control size and shape, and influence flowering or fruiting. It’s also necessary to prevent damage from storms, utility lines or other obstructions.
There are a number of different ways to prune trees depending on what type of outcome you want. Our professionals know the right cuts to make to achieve your desired results. Some methods, such as crown thinning and crown raising, help reduce the overall height of a tree while promoting healthy branching structure. Other techniques like reduction pruning and pollarding remove large limbs from the canopy of the tree to allow more sunlight through.
Regardless of what type of pruning is needed, our experienced tree service technicians will always be careful to avoid damaging the trunks and roots of your trees. In addition, we will always work within your property boundaries so that the trees we prune don’t damage your home, vehicles, sidewalks or power lines.
Most pruning is best completed from winter to early spring (before new growth starts). This helps wounds close faster and reduces the likelihood of insect and disease infestation. However, some types of pruning (like crown cleaning or reducing density) can be done at any time of year.
Some species, like birch, maple, dogwood, and elm, may exude excessive amounts of sap from pruning wounds in late winter or early spring. This is normal and can be avoided by pruning these species in late fall/early winter or after new spring growth is finished in May or June.
When pruning large, heavy limbs, it is important to follow a three-step process in order to not damage the tree while making the cut. Failure to do this can result in the tearing of bark several feet down the trunk of the tree. Failure to use this method can also cause the limb or trunk to break during removal. Whenever you are dealing with high, heavy limbs or if you have power lines near the area where you’re pruning, it’s always best to leave the job to the experts.
Tree Inspection
Trees are natural beauties, but they also pose a risk to people and property. If they become too damaged or diseased, they can fall, leading to structural damage and injuries. This is why it’s important to have them regularly inspected by professionals who can spot problems in time to prevent a disaster.
Tree service companies are trained to identify potential hazards and address them as quickly as possible. They have a deep understanding of local regulations and are aware of the legal responsibilities that come with owning or managing trees on public land. They also proactively secure the necessary permits and licenses for their operations. This ensures that their work is carried out safely and in full compliance with the law.
Emergency tree services are often called when a tree is in danger of falling. This can happen for a number of reasons, including storm damage, a pest infestation, or a root system failure. Regardless of the cause, a falling tree poses a major safety hazard and requires immediate attention.
Other signs that require a professional’s assessment include visible cavities in the trunk, fungal growth, insect infestations, or the separation of leaders. All of these are warning signs that a tree may be prone to failure and can result in serious injuries or damage.
A leaning tree is another common cause of emergency tree service. A tree that is leaning significantly can pose a threat to the structure of your home or other nearby structures and can lead to property damage or even personal injury. A leaning tree also indicates that the structural integrity of the tree has been compromised.
Regular inspections of your property’s trees can help you spot any potential issues before they become emergencies and save you money in the long run. Besides identifying problem areas, professionals can help you select healthy and suitable tree species that will thrive on your property and fit seamlessly into the landscape. They can also provide advice on pruning and other maintenance practices that will keep your trees healthy and reduce their risks.